全固体電池の量産化も見えた! 日産の次世代バッテリー生産最前線を取材、不可能を可能にしたブレイクスルーを解説
公開 : 2024.04.21 08:25
日産自動車は、神奈川県横浜市の横浜工場に全固体電池のパイロット生産ラインを設置する予定だとする。2024年4月、その建設中のパイロットラインがメディア向けに公開された。どのような内容であったのかを紹介する。
もくじ
ー車体の構造と生産方式の革新「次世代モジュラー生産」
ー全固体電池の課題と技術的ブレイクスルー
ー製造工程での全固体電池の課題とは
ー次世代の電動パワートレインのための技術
ーエンジンのマザー工場からバッテリーのマザーへ
車体の構造と生産方式の革新「次世代モジュラー生産」
建設中のパイロットライン見学の前に行われたのは、日産の現在進行中の技術開発の説明。
まずは、日産の執行役副社長である坂本秀行氏から、次世代EVの構造と生産方式の革新となる「次世代モジュラー生産」が説明された。
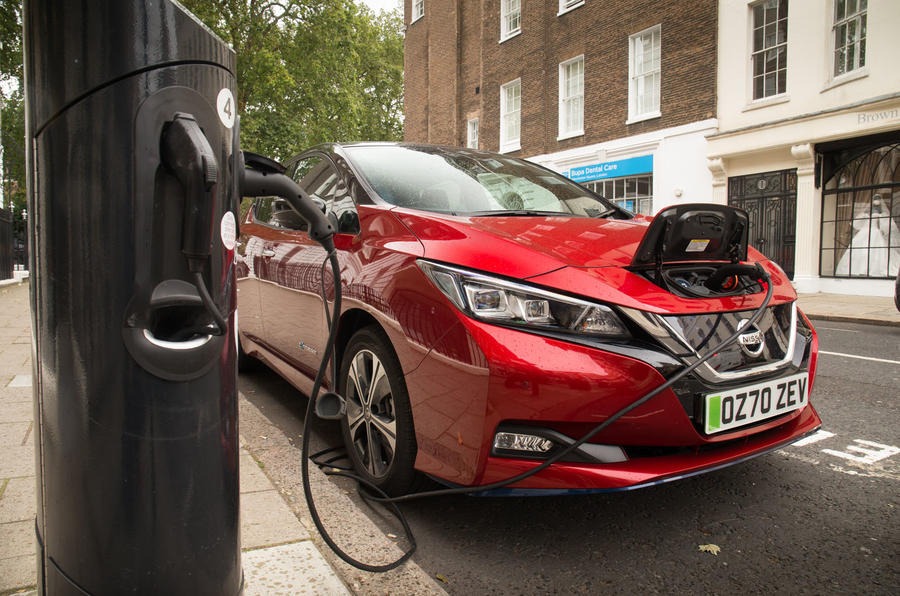
これは、床下に並べたバッテリーの上にシートなどの内装を取り付け、ボディは別工程でくみ上げる。最後にバッテリーと内装を装着した車両の下側と、上側のボディを合体させるというのだ。
従来のように、ボディを先に作り上げて、その後、作業員が中に入り込みながら部品を取り付けるのとは、まったく違う手順となる。
この工法の良いところは、露出しているバッテリーの上に内装部品を取り付けるため、労力が少ないという点にある。
また、メインラインが短くなり、細かな部品を先にくみ上げておくサブラインが長くなるのも特徴だ。この時、サブラインは労力が、さらに少ない。これにより、シニアや育児中の従業員などが、より働きやすくなるというメリットもあるという。
全固体電池の課題と技術的ブレイクスルー
続いては、常務執行役員であるパワートレイン・EVコンポーネント生産技術開発本部担当の村田和彦氏と、常務執行役員のパワートレイン&EV開発本部担当の生浪島俊一氏から、日産の全固体電池の開発状況の説明が行われた。
お2人の話をまとめると、現在は製品/生産技術開発のフェーズにあり、いくつもの技術的ブレイクスルーにて課題を克服している最中だという。
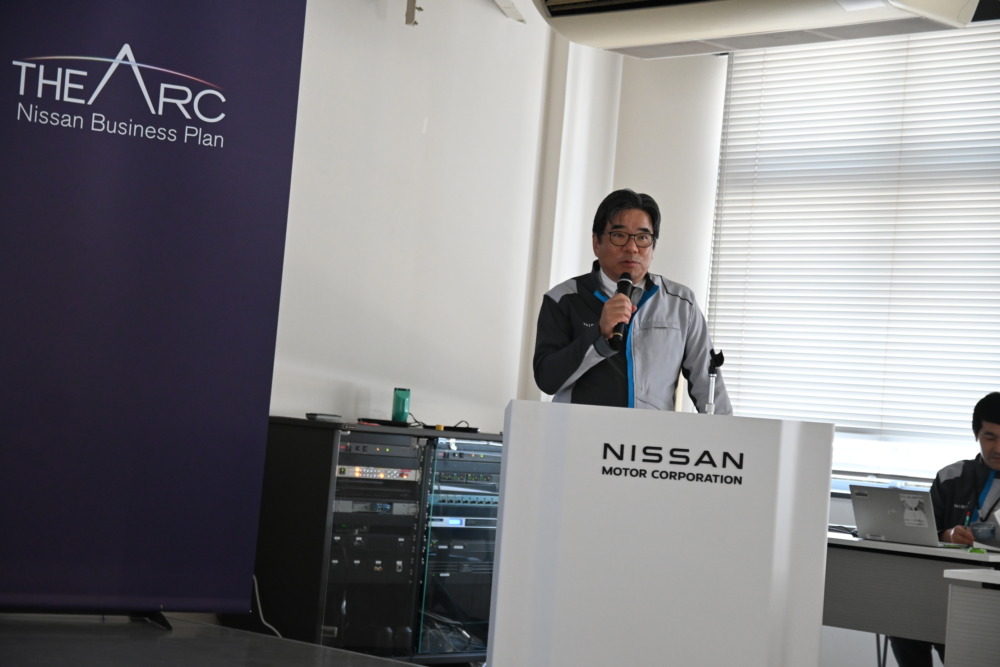
日産が開発する全固体電池は、硫化物固体電解質とリチウム金属負極を採用する。これにより従来の液体の電解質を使うリチウムイオンバッテリーよりも、性能面(1000Wh/L、充電時間短縮、熱に対する強さ、安全性、材料確保、コストなど)で、より優れた製品になるという。
材料面での課題として、硫化物固体電解質に使う複数の材料同士の接触面積の最大化というものがあった。液体を使う電解質なら、材料同士のサイズや形状が異なっていても、密着性に問題は起きない。
しかし、固体の場合はそれに困難であるため、繊維状バインダー(接着剤)を使うことで解決したという。繊維状のバインダーは隙間が大きいため、リチウムイオンの移動を阻害せず、材料同士の密着度を高めてくれるというわけだ。
製造工程での全固体電池の課題とは
製造工程でも課題がある。日産の全固体電池の製造では、材料を薄いシートにして、正極/固体電解質を重ね合わせている。そうしてできた全固体電池は、充電すると正極にあったリチウムが固体電解質を経由して負極側に析出する。負極側にリチウム金属層が生まれるのだ。逆に放電すると、負極側のリチウム層がなくなる。つまり充放電で負極側のリチウム層ができたり、消えたりするのだ。
この時、重要なのが、負極側に析出されるリチウム層が「均一」であることだ。うまくいかないと短絡(ショート)や劣化が進んでしまう。
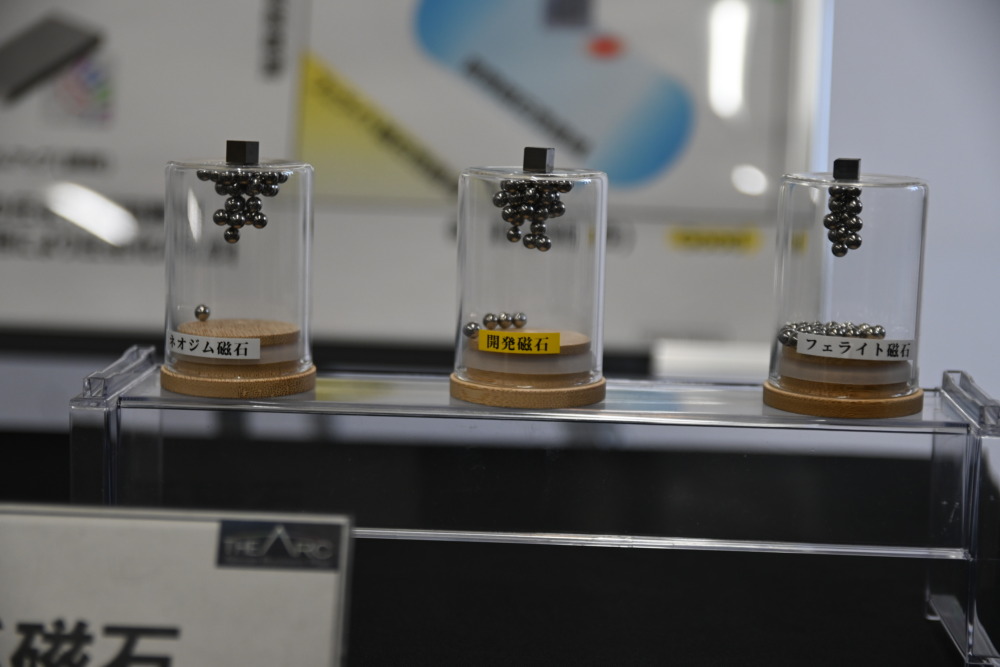
それを防ぐために、平滑で科学的に均一な電極を作り出す、材料の混ぜ合わせ方や加圧方法を生み出したという。また、充放電での電池の体積変化に対応するバッテリー全体の新機構もブレイクスルーの一つとなる。
そして、最後の製造工程の技術的ブレイクスルーは、効率的な超低露点環境の構築だ。低露点環境とは、湿度の少ない環境のこと。リチウムイオンバッテリーの製造は、空気中の水分を除去した部屋で行う必要がある。その環境を作り出すのに、非常に多くの電力を消費していた。
それを、超低露点空間を一部に限ることと、気流をコントロールすることで、空調の電力使用量を大きく削減したというのだ。
コメント