ポルシェ・クラシック、3Dプリンターから9種のパーツ供給 追加20種の検討も
公開 : 2018.02.14 16:20 更新 : 2018.02.14 16:27
959のリリースレバーができるまで
ポルシェ959のクラッチのリリースレバーを製造するためには、まずコンピュータ処理によって厚さ0.1mm以下の粉末工具鋼の層で処理プレートを覆う。そして、不活性ガスの中で、高エネルギーのライトビームを用いて希望する場所で粉末を溶融させ、スチール層を作り出すのだ。
こうして、一層ずつ完全な3次元コンポーネントが製造される。プリントされたリリースレバーは、3t近い負荷をかけた圧力試験と、その後の内部欠陥を調べる断層撮影法による検査にもクリアした。
最後に、テスト車両に取り付けられたレバーを用いた実地試験と徹底的な走行試験により、コンポーネントの完璧な品質と機能が確認された。
他8つのパーツを製造中 さらに20の製造検討
これまで一貫して肯定的な結果が得られてきたことを踏まえ、現在ポルシェでは3Dプリントを使って他に8つのパーツを製造中だという。
具体的には、レーザー溶融法を用いて製造されるスチールおよび合金製のパーツと、SLSプリンターを用いて製造される樹脂製コンポーネントだ。
「SLS」は「レーザー焼結法」の略で、これは融点の直前まで材料を加熱し、残余エネルギーを用いレーザーで目的とする箇所の樹脂粉末を溶解するという方法。全パーツとも、最低でも元の製造期間の品質要件が課せられるが、通常はさらに高い基準がクリアされる。
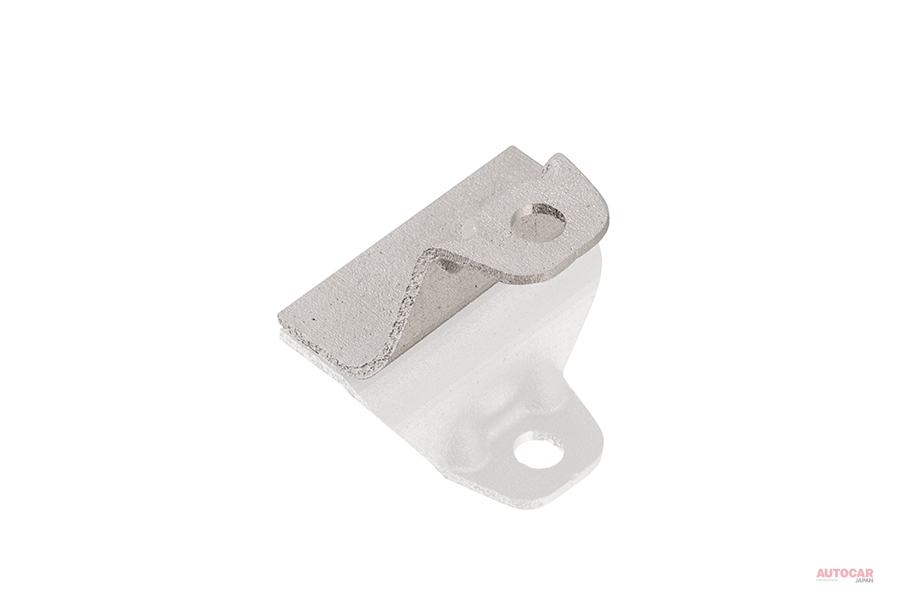
取り付けたパーツを用いて試験することで、寸法と嵌め合いの精度が確保される。適用分野によっては、オリジナルと同様、多様な材料で作られた樹脂製パーツは、オイル、燃料、酸、光への耐性を有する必要がある。
現在、ポルシェ・クラシックでは、さらに20のコンポーネントの製造についても3Dプリントが適切であるかどうか、試験している最中だという。
メリットは、コンポーネントの3次元デザインデータや3Dスキャンがあれば、製造を開始するための十分な基礎となること。必要に応じて、注文があり次第コンポーネントを製造できるため、ツールと保管コストの節約にもなる。
なお、AUTOCAR JAPAN上でこの記事をご覧になっている方は、記事下の「すべての画像をみる」ボタンから、外部メディアでこの記事をご覧の方は、記事下に設けられたリンク「『3Dプリンターで制作されたパーツ』すべての画像をみる」から、ほかの画像をお楽しみいただける。