【新型ディフェンダーの故郷】JLRスロバキア工場を訪問 新たな時代の幕開け
公開 : 2020.02.22 18:50
どんな不具合にも対応
クラッソンは、「アルミニウム製骨格を採用したことによるメリットは、溶接よりもその組立工程がクリーンで静かだということです。ですが、リベットによる固定には高い精度が要求され、それは溶接の比ではありません」と、話す。
ボディショップで唯一人間が主役となるのが、ドアとフェンダー、ボンネット、そしてトランクリッドの取り付け工程だ。
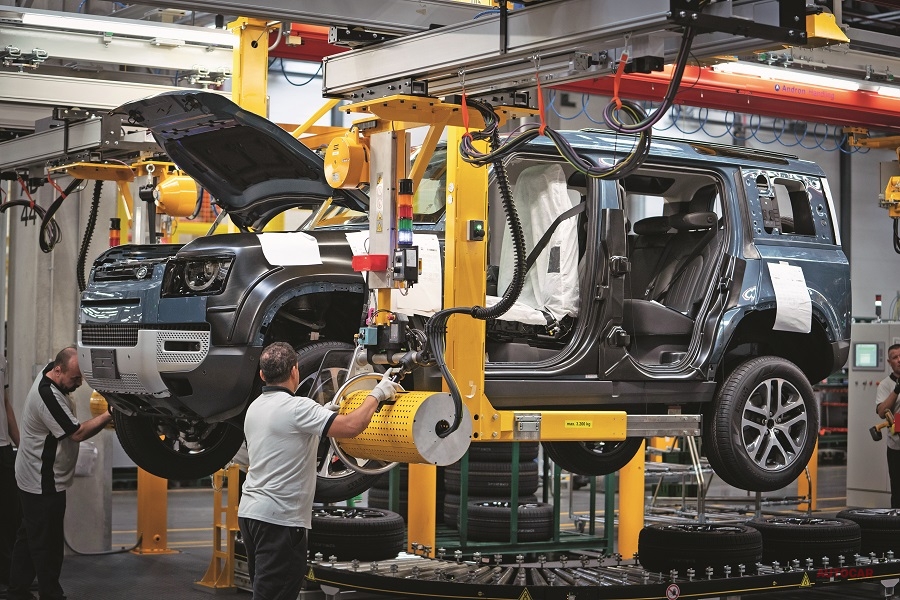
すべての工程が完了すると、組み上がったボディは厳しいチェックを受けることになる。
「どんな不具合にも対応出来るようステーションが3つ用意されています」と、クラッソンは言う。
「英国のラインははるかに長いものでした。初めてあるべき姿を実現出来たことを誇らしく思っています」
時間が足りないのでペイントショップをパスして、13万4000平方メートルという圧倒的な敷地面積を誇る内装と最終工程の建屋へと向かうことにした。
ここでは最初にインテリアの組み付け作業が容易に行えるよう、ドアが取り外される。
そして、何よりも注目すべき存在が、ガラスを持ち上げ、糊付けをし、1分以内にサンルーフを所定の場所にセットすることの出来るガラス組み付けロボットだろう。
内装と最終組み立てで責任者を務めるウラス・バグチが、エンジンとラジエーター組み付けなどの主な工程を説明してくれた。
「ここでボディとエンジンが初めて組み合わせられるのです」と、彼は言う。
新たな経験 学び続ける
生産ラインに250あるステーションのそれぞれに、目立たない黄色のロープが設置されているが、このロープを1回引くとチームリーダーが手伝いに、2回引くとラインがストップするようになっているのだ。
「2分間の作業の途中でラインがストップするとその影響は甚大です」と、バグチは言う。
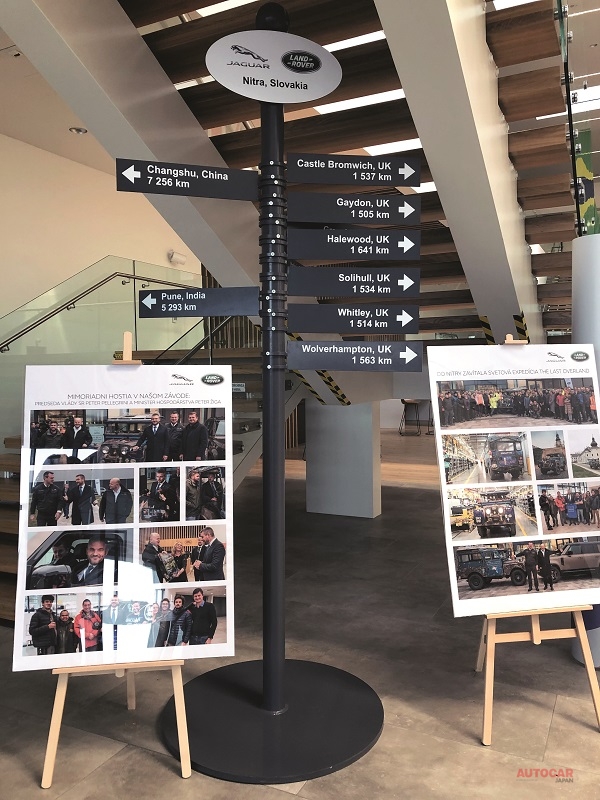
だが、組み立て工程全体で最大の課題は、「ボトルネックとなっているのが非常に複雑な電子機器類の組み付けです。すべては電子制御です」と、彼は話している。
最後にレスリーは、「新型モデルの生産開始はつねに新たな経験です。ましてや、新たな国で新たなチームであればさらなる困難が付きまといます。学び続けるだけです」と、話している。
「新型ディフェンダーのデザインとエンジニアリングは英国で行われていますが、新型モデルの生産を新工場で行ったのは初めてのことでした。それでも、スケジュールどおりの立上げに成功し、需要に応じて生産台数を伸ばしています」
われわれが工場見学を終えると、ちょうど数百人のオペレーターがシフトの交替に合わせてJLRがアレンジしている7台のバスから続々と降りてきた。工場へと彼らを運ぶ公共交通機関がまだ整備されていないのだ。
この状況に対処すべく、地元行政との対話が続けられているというが、生産ラインに求められる完ぺきさを知った後では、スロバキアの公共交通が英国よりも正確であることを祈らずにはいられない…
コメント