90年、4000万基のエンジンを生産 日産横浜工場で最新の生産過程を見学
公開 : 2023.11.21 20:05
数々の最先端の技術を採用して課題をクリア
生産に数々の難しさを抱えるのがVCターボだ。そのためVCターボの生産に関して、日産では、数々の最先端技術を採用した。
その筆頭が、SUSミラーボアコーティングだ。シリンダーの鋳鉄ライナーを廃し、そのかわりに溶かしたステンレスをシリンダーボア内に吹き付けて、さらに鏡面に磨き上げる。これにより、ピストンの摺動位置変化を許容するだけでなく、フリクションの低減、軽量化(4気筒エンジンでマイナス2kg相当)、熱伝導性能アップによる耐ノック性能アップが実現する。
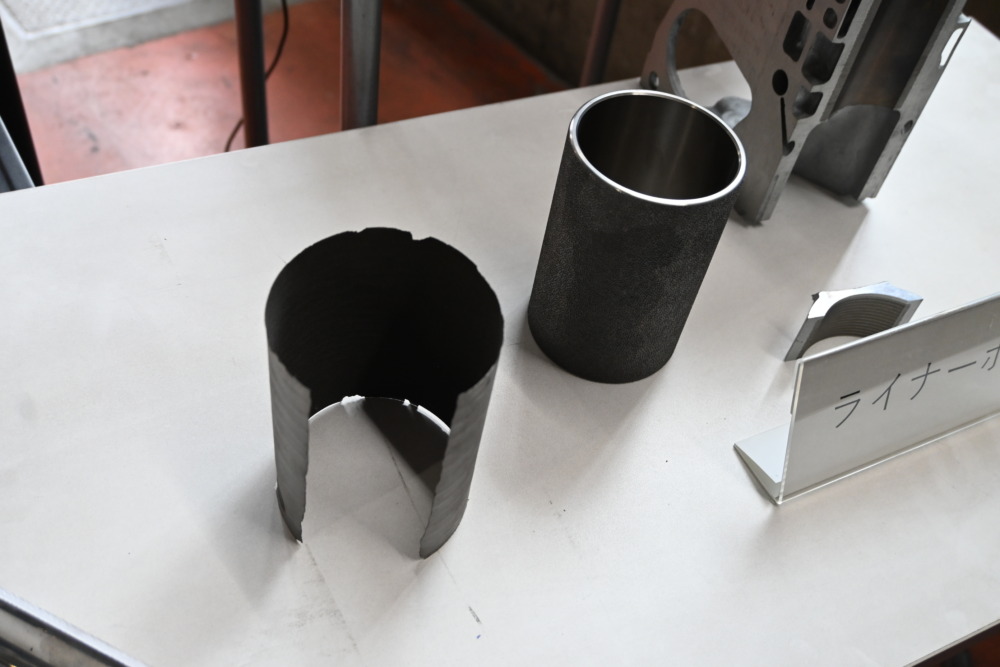
また、コントロールシャフトに続くCリンクの検査用に、メタルクリアランス自動保証を採用した。これまで熟練工が手で行っていた検査作業をロボットに覚え込ませて、全量を検査するのだ。また、完成後は圧縮空気をシリンダー内に吹き込み、疑似的にエンジンを燃焼させた状態にして動かすリンクテスターも行っている。
さらに通常エンジンの約1.9倍の荷重がかかるLリンクには、HRC60というヤスリよりも硬くなる表面加工を実施。組み立てには、専用器具にて約2tもの力で圧入を行っている。加工が難しいだけでなく、組み立てにも高い精度が求められるLリンクは、可変圧縮機構の要ともいう部品だ。
そのためVCターボの生産は、日本だけでなく中国や北米でも行われているが、Lリンクの製造だけは、日本の横浜工場/いわき工場/日産工機(株)で実施。部品を海外の工場へ供給しているという。
自動化された機械が作業を行う
今回は、SUSミラーボアコーティング、メタルクリアランス自動保証、Lリンクの組み立ての現場を見学した。
最初に赴いたのはSUSミラーボアコーティングの現場だ。天井の高い、広い、いかにも工場といったスペースに、巨大トレーラーヘッドのような箱型の加工機器が並んでいる。横に設置されたロボットアームが、運ばれてきたシリンダーヘッドをひとつずつ加工機器の中に納める。
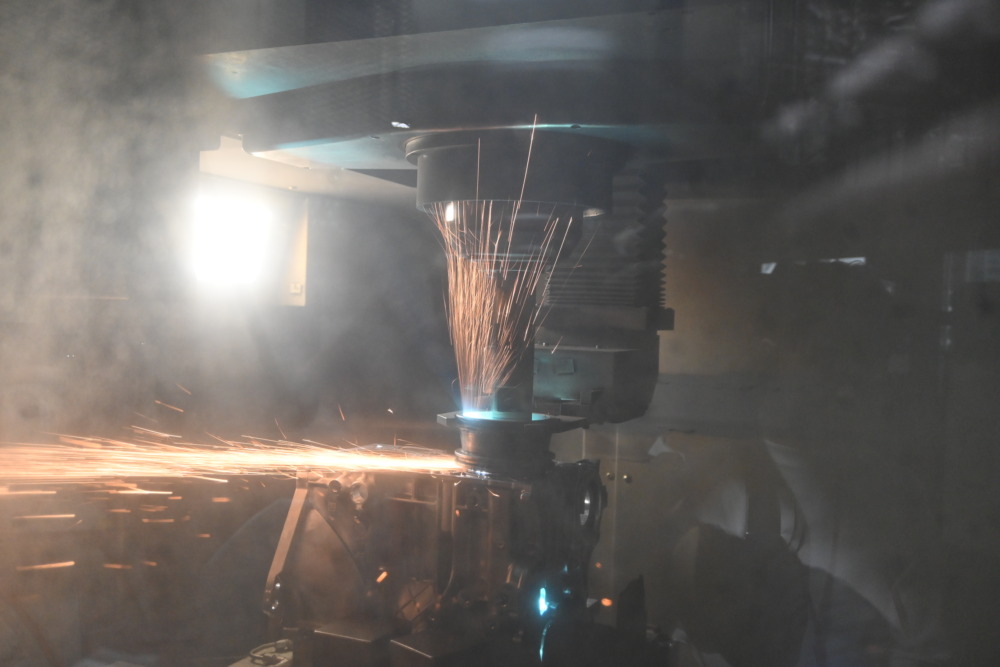
最初にシリンダーボア内の表面を削る。この下処理があることで、吹き付けたステンレスが強く固着できるというのだ。
削られたシリンダーは、ロボットアームによって隣の加工機器に移動される。そこで溶けたステンレスが吹き付けられる。高温の鉄を吹き付けるため、加工機器の窓からは、シリンダーに飛び散る火花が見える。
吹き付けの終わったシリンダーヘッドは、さらに別の加工機械の元へ。そこでは冷却水をじゃぶじゃぶとかけながら、シリンダーボア内の磨き上げが行われる。ここまでの加工時間は、すべてが自動で、わずか10分ほどであった。
コメント