90年、4000万基のエンジンを生産 日産横浜工場で最新の生産過程を見学
公開 : 2023.11.21 20:05
空調の効いた別室で組み立てを行う
続いては、Lリンクの組み立てとメタルクリアランスの自動保証。こちらは、空調の効いた涼しい別室で実施される。温度変化による部品の膨張・収縮を防ぐのが空調の理由だ。7月の酷暑の最中での見学でも、この現場はオフィスビルのような快適な空間となっていた。
Lリンクの組み立ては、部品を作業員が治具にセットするだけ。あとは機械が自動で圧入を行っていた。
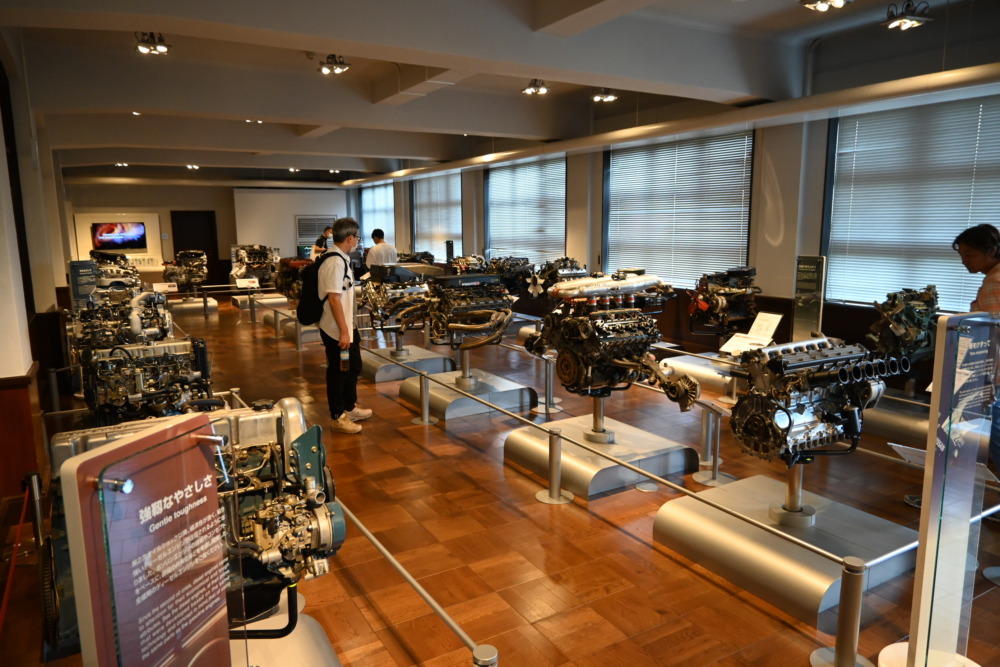
また、Cリンクのメタルクリアランス自動保証とは、組み立ての終わった部品のクリアランスをロボットが行うというもの。そこで許されるクリアランスの誤差は、従来エンジンの半分ほどとか。厳密な検査が、ロボットの手によって粛々と進められていたのだ。
建屋は古いけれど、生産設備は最先端であり、広々とした余裕あるレイアウトであった。また、組み立てラインを見ていないこともあってか、作業する人が少なかったのも印象に残った。
創業の地ということで、ゲストホールは旧本社ビルであり、横浜市より歴史的建造物に認定されている。エンジンミュージアムを擁するなど、歴史を感じさせる建屋であった。また、工場も建屋自体は、相応に古びていたが、中に置かれた機器類や作業の内容は、まさに最先端。日産の今を感じさせるものであった。そのアンバランスも今回の見学の醍醐味のひとつだったと言えるだろう。
コメント