【5年以内に量産か】ポルシェ、3Dプリント技術でピストン開発 911 GT2 RSで検証、パワーアップも
公開 : 2020.07.29 11:50
3Dプリント技術の採用により、ポルシェは911 GT2 RSの性能をさらに引き出すことに成功しました。エンジンのピストンを3Dプリントすることで冷却効率と軽量化を実現。回転数を高め出力向上につなげました。
軽量化により約30psアップ
3Dプリントの技術は、数年前から自動車部品の試作品製作に利用されてきたが、生産部品の製作にも利用されるようになってきた。
ポルシェは、エンジンの中で最もストレスのかかる部品であるピストンの3Dプリントに成功した。テスト機は、991世代の911 GT2 RSである。
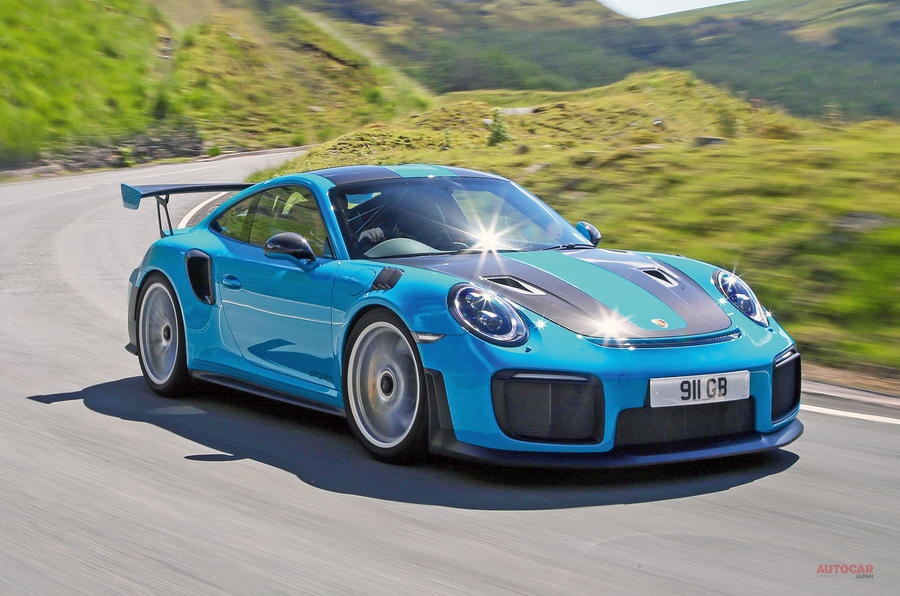
このピストンは従来部品よりも10%軽量化されており、エンジンの回転数を300rpm上げることで、約30psのパワーアップに貢献している。
荷重や熱による大きな応力を受ける高性能エンジンのピストンは、通常はアルミ合金から鋳造または鍛造される。
ポルシェは、ドイツの部品メーカーであるマーレや、プリンターメーカーのトルンプと協力して、最先端のレーザー溶融法を開発した。
設計コンピューターから直接取得したデータをもとに、粉末状のアルミ合金を1層ずつ1200層に分けて融合させることで、ピストンが形成される。
トポロジー最適化ソフトウェアを使用して、力が大きくなる部分を特定し、素材の量が正確に使用されるようにする。
合金がレーザーの熱で高温になっている間、たるみや変形を防ぐために、一時的な支持構造がピストンの設計に組み込まれている。
この支持構造は、後に機械加工されるピストンのピンホールのような部分の内側に、ハニカムのように形成されている。除去作業の省略につながる仕組みだ。
溶融した金属を型に流し込む従来の鋳造技術や、プレスで形を整える鍛造技術では不可能な新しい機能をデザインに組み込むこともできる。
ポルシェはこのメリットを活かし、ピストンの外周を走るトンネルのような内部冷却ダクトを導入した。
工数に改善の余地 12時間で5個
このダクト内を流れる冷却オイルは、ピストンとシリンダーをシールするピストンリングの後ろの重要な部分で、ピストンの温度を20℃下げるという。
ダクトには、3Dプリントされた小さなオイルジェットが備わっているが、複雑すぎて従来の技術では作ることが難しい。

このソフトウェアは、自然界に見られる「バイオニック」デザインを利用して強度を高めている。ピストンの断面図は、筋肉や筋の集まりのように見える。
現在の生産体制では12時間で5個のピストンを作ることができるが、より洗練されたプリンターを使えば、3倍の15個に増やすことが可能だという。
試作品は911 GT2 RSのエンジンでテストされており、平均時速250kmで6000km、サーキット走行を135時間のアクセルべた踏みを含めて200時間シミュレートしている。
現段階では高価な工法であり、一貫した品質を確保するためには改善が必要だが、この技術は今後5年以内に量産車のエンジンに利用される可能性があるという。